PaulCee
Member Since: 31 Oct 2014
Location: UK
Posts: 18

|
Firstly thank you to everyone who has helped me recently.
I bought a 4.4 TDV8 AB a couple of months ago for my wife, after she had a TD6 for the last 9 years. I wasn’t thinking of changing but this one came up and peaked my interest. Anyway TDV8 bought, TD6 sold and that leads to where I am now.
I knew there were some issues that I needed to fix with it, and I am one of those people who likes to get involved, and after that if I find I can’t, then off to my local indy.
So faults were, so I thought, oil leak back of the engine, some paint work on bonnet, little bit of rust starting to surface on underside of rear tailgate. Not too bad.
There ended up being a few more jobs than that which I will list at the end, but one of these “new jobs” was EGR temp sensor. So I read through the excellent wiki from GGDR, Greg and the the comments that followed and managed to complete it over a few days. I wasn’t at it all the time, there were many breaks and “how am I going to get my hand on that” moments, but I found these breaks and a cup of tea helped.
I only used Gregs steps just as a reference and how each of these went for me.
Step 1 was as Greg says find the sensor and over the next week I lubed with Plusgas. I found the best way to achieve this was endoscope camera (the endoscope camera proved vital for most tasks, due to no vision once my arm was down the side of the engine), and a three small straws taped together with tin of Plusgas on the end, as per instructions. It was difficult to spray all around the sensor nut as the top is under the incline of the engine, so I filled the centre where the sensor is, and it overflowed evenly running down the sides of the nut. I did this all week, once a day.
Step 2. Remove the pollen filter air box, battery surround. The cable for my sensor was already unclipped from its clips and looking at the heat shield, this sensor had been changed before. Unplugged sensor wire.
Step3. My step 3 was to cut the top of the sensor before the shield movement, as I figured this would give me better access to the retaining bolt for the heat shield, right next to the sensor. This proved to be one of the biggest hold ups for me. Tried hack saw blade, then I ordered Dremel type tool with Flexi shaft (like aids22) to cut it, but scared me how close the sensor top was to the hard pipe, and how this would give me another job if I messed up. So ordered small bolt cutters, but again a problem as the arms had to open so wide I could not find a way to get them in. Finally back to a hacksaw blade and persevered. Took a while but finally did it .
Heat shield bolt was then very visible and easy to remove with a socket, 300mm extension and ratchet.
 | Click image to enlarge |
Step4. Now I must thank J9ffy for making my life so much better with the invention of long piece of wood and a screw in the end. Once I had the bolt out of the heat shield by the sensor, and this is the only bolt I took out for the heat shield by the way, the screw in the end in the piece of wood caught under the heat shield and pulled it up and away from the sensor area, I then used the other end of the wood to push it away further, and then that was it done. 2 minutes work.
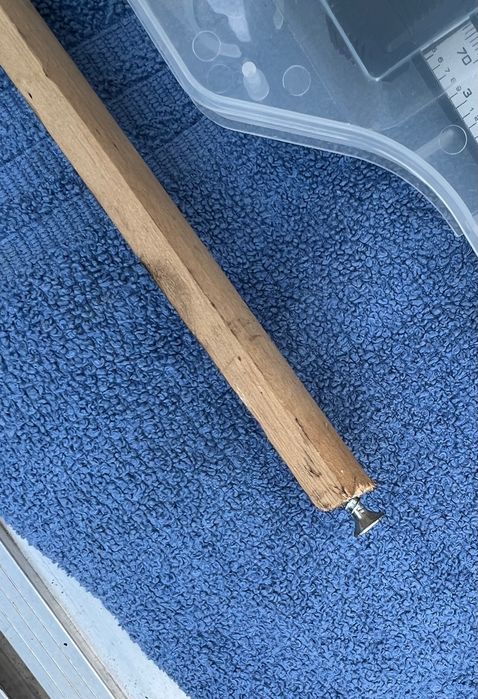 | Click image to enlarge |
Step 5. Tried both the long socket and the short. With both of them I used aids22 idea , he used for putting the head shield screw back in. I used cotton to lower the socket down and then my fingers to guide it onto the nut of the sensor. In the end I used the small socket as I could feel it better and how it was sitting on the nut, which I thought was important. Now was the time to try and turn the nut, I used a 3/8 flexihead ratchet, with a 3/8 to 1/2 adapter, a small extension and the socket. The flexihead also had an extendable handle. I left the socket in place on the nut and lowered the ratchet and connected the extension to it. Checking everything again to make sure, and all seemed solid. I had enough room to put pressure on the top of the ratchet with my free hand, whilst I turned the ratchet antilock wise with the other. First go nothing, then second with a bit more force it cracked. Once it started to move it really needed very little force, and I swapped out the ratchet etc for the smaller 1/4 ratchet an 300mm bar and socket. Nut came off (picture below) sensor needed a tap to get loose. I would also say that the week long lubrication did work. The threads of the nut were wet from Plusgas, and the end of the temp sensor was wet again, and it was Plusgas. It might be as I used almost a small tin of the stuff over the week.
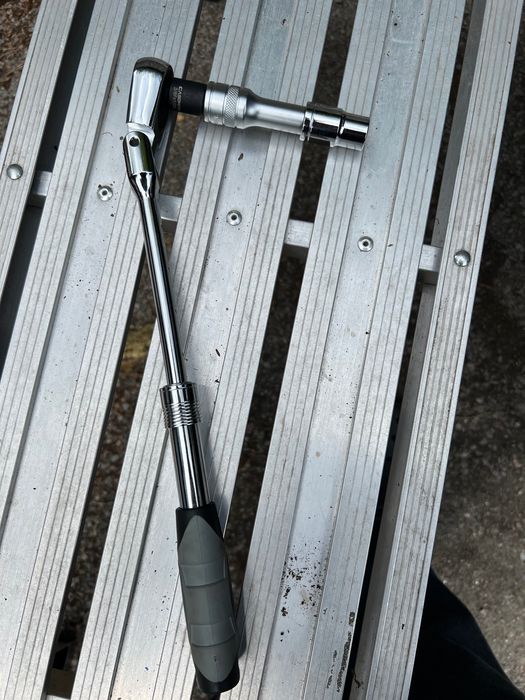 | Click image to enlarge |
Step 6. Tried to do this but so difficult to reach with Q-tips. Tried a couple of times and it did clean things but worried about dropping them in the hole I was cleaning. So only minimal cleaning done. Tried putting the old nut in but again my fingers are too short, I could just about touch the nut with fingertips, and kept dropping. Thankful for cotton tied to it, not so much for the old temp sensor as I dropped that and lost in the engine.
Step 7. This was another problem. As I said I could only just touch the nut of the sensor, so once I had lowered the sensor in the hole, trying to get the correct angle, and rotate the nut with the last bit of your finger tips was difficult. All you can do is keep going and eventually the nut grabs. Then you are worried it’s maybe crossed threaded. Again the endoscope camera showing what’s going on was just invaluable. You could see the nut was looking straight for example, so on with the laser tools socket. Also did apply anti seize, just in case I’m lucky enough to have to do it again!
Got to this point, where the laser socket was needed, and like some others it was too small. Testing it on the old nut and it would not fit. So more time taken with crow bar to open up socket, hammer to close, whilst old nut is inside. Then after a few repeats of this process it works. I definitely do not recommend the laser tool spanner.
Slipped it onto the sensor, using cotton again, and tightened until it started to feel like the socket starting to flex a bit. So I called this tight. (I could not get my torque wrench in there either). I also worried about the nut properly seating against the block, as there was a gap. But after asking (thank you graryRR) and looking at the old nut, the thread does not go all the way to the top, so this is probably the reason.
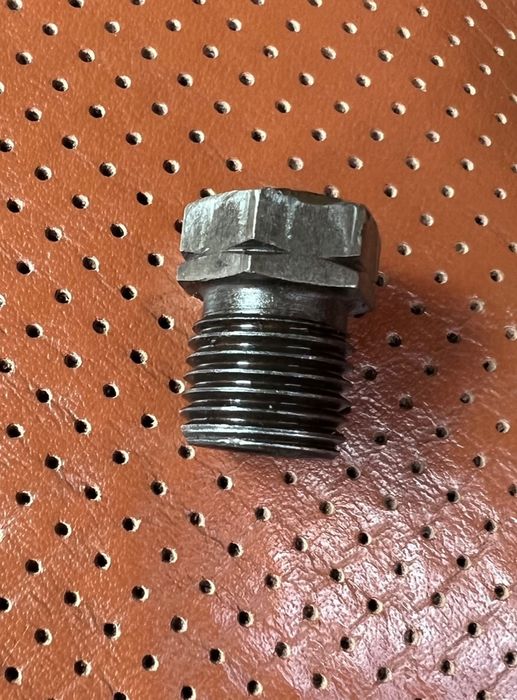 | Click image to enlarge |
Step 8. Used my favourite tool of a bit of wood and screw in the end, to flatten heat shield. I used the blunt end this time without the screw and it folded back where it was meant to be, being careful to miss the sensor. The was also a lifted ridge in the middle where the heat shield had folded back on itself, but a push with the piece of wood flattened it. Again 2 minute job.
The only remaining tricky bit was did the bolt now line up with the hole after the flexing of the heat shield. For this I used again 1/4 wrench, 300mm extension and socket, much like I had done to remove. This time though I had to avoid the sensor top. I loaded socket with grease to keep bolt in place, and pushed “New” bolt into it as I dropped the original. Bolt went in first time and bit into the thread on second rotation, whilst trying to get angle right. Job done.
Before final reassembly plugged in sensor and scanned, and what a great feeling that is, code gone.
This is just my experience and is not meant to be any sort of guide, and I have only written it as it may help someone, as other peoples’ experiences have helped me.
Hands and arms a little bruised, and you can’t really explain correctly how little movement there is for your sole hand that can fit down the side of the engine. I also tied my tools to my wrist, which saved me a few times, and gave me confidence to try things as it did not matter if they dropped.
Once again thank you Greg GDDR, not been possible without your guide.
So just to finish, I have now done
“O” Rings on Pipe to Rear of Engine for Oil Leak
Oil Cooler Gaskets
Change Oil and Coolant
Throttle Body Gasket
Throttle Body Clean
EGR Tube degunk
Clean MAP and MAF Sensors
Replace Plenum Hoses
Replace water pipe with “fragile” hose.
Repaired loose Solid Plastic inlet by large “O” ring method (guide from this site)
Replaced small hose from Solid Plastic inlet to solid pipe
It's keeping me busy.
Just and O2 sensor left to do, …..for the moment. 2011 Range Rover AB 4.4 TDV8
|